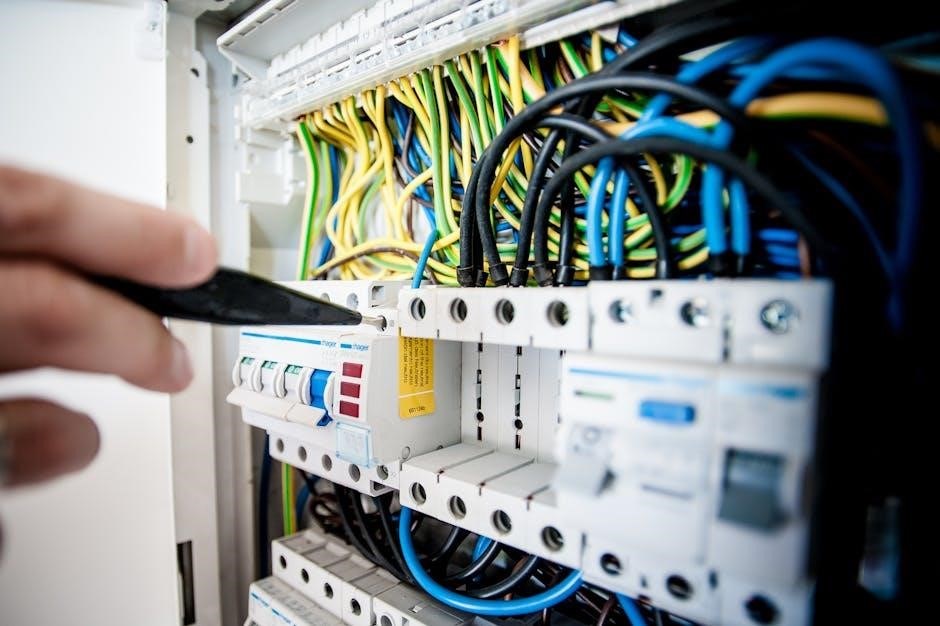
basic hydraulic circuit diagram pdf
A hydraulic circuit diagram is a visual representation of a hydraulic system‚ showcasing components and their connections. It simplifies understanding‚ designing‚ and troubleshooting fluid power systems effectively.
1.1 What Are Hydraulic Circuit Diagrams?
Hydraulic circuit diagrams are detailed visual representations of hydraulic systems‚ illustrating components like pumps‚ valves‚ and actuators. They use standard symbols and graphical elements to depict fluid flow paths‚ connections‚ and system operation. These diagrams simplify understanding complex hydraulic systems‚ aiding in design‚ analysis‚ and troubleshooting. They are essential for conveying how components interact to achieve specific functions‚ ensuring efficient system performance and proper installation.
1.2 Importance of Hydraulic Circuit Diagrams
Hydraulic circuit diagrams are crucial for understanding and analyzing hydraulic systems. They provide clarity on component interactions‚ fluid flow‚ and system operation‚ ensuring efficient design and troubleshooting. These diagrams standardize system representation‚ facilitating communication among engineers and technicians; They are essential for identifying potential issues‚ optimizing performance‚ and ensuring safety. By visualizing the entire system‚ hydraulic circuit diagrams simplify complex processes‚ making them indispensable for maintenance‚ operation‚ and education in fluid power systems.
Hydraulic Symbols and Circuit Representation
Hydraulic symbols standardize component representation‚ enabling clear visualization of fluid flow and system functionality. These symbols are essential for designing and interpreting hydraulic circuit diagrams accurately and efficiently.
2.1 Standard Symbols in Hydraulic Circuit Diagrams
Standard symbols in hydraulic circuit diagrams represent components like pumps‚ valves‚ cylinders‚ and reservoirs. These symbols‚ often defined by ISO standards‚ ensure consistency and clarity in system design. They depict flow paths‚ pressure points‚ and control mechanisms‚ aiding in the creation and interpretation of circuit diagrams. Proper use of these symbols simplifies communication among engineers and technicians‚ ensuring accurate system assembly and operation. Each symbol corresponds to a specific function‚ making hydraulic systems easier to understand and maintain.
2.2 Graphical Illustration of Hydraulic Circuits
Graphical illustrations of hydraulic circuits use standardized symbols and diagrams to visually represent system components and their interactions. These diagrams often include flow paths‚ pressure points‚ and control mechanisms. Cutaway diagrams reveal internal component structures‚ while block diagrams simplify complex systems into functional segments. Colors and patterns may indicate pressure levels or fluid conditions. These visual tools enhance understanding and communication‚ allowing engineers to design‚ troubleshoot‚ and maintain hydraulic systems effectively. Clear illustrations ensure accurate interpretation and efficient system operation.
Basic Hydraulic Circuit Design
A basic hydraulic circuit design involves essential components like pumps‚ actuators‚ and control valves‚ ensuring fluid flow and pressure are effectively managed for system functionality.
3.1 Types of Hydraulic Circuit Configurations
Hydraulic circuits are configured in various ways to suit specific applications. Open-loop systems are simpler‚ with fluid flowing from a pump to an actuator and back to a reservoir. Closed-loop systems recirculate fluid‚ offering precise control for applications requiring constant pressure and flow. Series circuits connect components one after another‚ while parallel circuits allow multiple actuators to operate independently. Each configuration is designed to optimize performance‚ efficiency‚ and control‚ ensuring the system meets its operational requirements effectively.
3.2 Essential Components of a Hydraulic Circuit
A hydraulic circuit consists of key components that enable fluid power transmission. The pump generates fluid flow‚ while actuators convert hydraulic energy into mechanical work. Valves control fluid direction and pressure‚ ensuring precise operation. A reservoir stores hydraulic fluid‚ and conductors like hoses and pipes transport it between components. Sensors and filters are also crucial for monitoring and maintaining system performance. Each part plays a vital role in ensuring the circuit operates efficiently and safely‚ meeting the system’s functional requirements effectively.
Fluid Power Basics in Hydraulic Systems
Fluid power in hydraulic systems relies on transmitting energy through pressurized fluid. Hydraulic fluid transfers force‚ enabling tasks like lifting or moving loads efficiently in industrial applications.
4.1 Role of Hydraulic Fluid in Circuit Design
Hydraulic fluid is the medium that transmits energy in a hydraulic system. Its properties‚ such as viscosity and compressibility‚ directly impact system performance and efficiency. The fluid must lubricate components‚ transfer heat‚ and maintain seal integrity while withstanding pressure and temperature variations. Proper fluid selection ensures optimal system operation‚ preventing wear and extending equipment lifespan. Designers must consider fluid compatibility with system materials and operating conditions to avoid degradation or contamination. The fluid’s role is critical in enabling smooth‚ reliable operation of hydraulic circuits.
4.2 Fundamental Principles of Hydraulic Systems
Hydraulic systems operate based on fluid mechanics principles‚ where fluid pressure and flow are utilized to transmit energy. Pascal’s Law underpins hydraulic operation‚ stating that pressure applied to a fluid is uniformly distributed. The system converts mechanical energy into hydraulic energy via pumps‚ which create fluid flow and pressure. This energy is then transferred to actuators‚ such as cylinders or motors‚ to perform work. The relationship between fluid flow‚ pressure‚ and system resistance governs the overall performance and efficiency of hydraulic circuits‚ enabling precise control of motion and force.
Open-Loop vs. Closed-Loop Hydraulic Circuits
Open-loop circuits are simpler‚ with fluid flowing in one direction and returning to the tank. Closed-loop systems recirculate fluid‚ enabling precise control over pressure and flow rates for demanding applications.
5.1 Open-Loop Hydraulic Circuits
Open-loop hydraulic circuits are the most common type‚ where fluid flows in one direction and returns to the reservoir after completing the circuit. These systems are simpler in design‚ with fewer components‚ making them cost-effective and easier to maintain. In open-loop circuits‚ the pump supplies fluid to the valve and actuator‚ and excess fluid bypasses back to the tank. They are ideal for applications where precise control over pressure and flow is not required‚ such as in basic machinery and hydraulic lifts.
5.2 Closed-Loop Hydraulic Circuits
Closed-loop hydraulic circuits continuously recirculate fluid‚ offering precise control over pressure and flow. These systems are used in applications requiring high accuracy‚ such as CNC machines and robotic systems. In a closed-loop circuit‚ the pump delivers fluid to the actuator‚ and the return line directs it back to the pump‚ maintaining consistent system operation. This design minimizes energy loss and enhances efficiency‚ making it ideal for demanding industrial applications where tight control and reliability are essential.
Hydraulic System Block Diagrams
Hydraulic system block diagrams simplify complex systems into functional blocks‚ showing interactions between components like pumps‚ valves‚ and actuators. They aid in designing and analyzing system operation efficiently.
6.1 Block Diagram of a Basic Hydraulic System
A block diagram of a basic hydraulic system illustrates the functional structure‚ highlighting key components like the reservoir‚ pump‚ directional control valve‚ and cylinder or actuator. The reservoir stores hydraulic fluid‚ while the pump generates the necessary pressure and flow. The directional control valve directs fluid to the actuator‚ enabling movement or operation. Sensors and feedback mechanisms may be included to monitor system performance. This simplified representation helps in understanding the flow of hydraulic fluid and the interaction between components‚ making it easier to design‚ analyze‚ and troubleshoot the system effectively.
6.2 Functional Structure of Hydraulic Systems
Hydraulic systems are functionally structured into three primary sections: power supply‚ control‚ and actuator. The power supply section includes the reservoir and pump‚ providing the necessary hydraulic fluid and pressure. The control section consists of valves that regulate fluid flow and direction. The actuator section‚ such as cylinders or motors‚ converts hydraulic energy into mechanical work. This structured approach ensures efficient energy transmission‚ precise control‚ and effective operation‚ making it easier to design and troubleshoot hydraulic circuits.
Hydraulic Circuit Operation and Control
Hydraulic circuits operate by transferring energy through pressurized fluid‚ controlled by pumps‚ valves‚ and actuators‚ enabling precise mechanical tasks in various applications.
7.1 Operation of a Double-Acting Hydraulic Cylinder
A double-acting hydraulic cylinder operates by allowing hydraulic fluid to enter and exit both ends of the cylinder‚ enabling bidirectional piston movement. In one direction‚ fluid flows into the cylinder through one port‚ extending the piston. When the control valve directs fluid to the other port‚ the piston retracts. This process is controlled by directional control valves‚ ensuring smooth and precise operation. The double-acting cylinder is widely used in applications requiring both push and pull forces‚ making it a fundamental component in hydraulic systems for machinery and automation.
7.2 Control Methods in Hydraulic Circuits
Control methods in hydraulic circuits regulate fluid flow‚ pressure‚ and direction to achieve precise system operation. Directional control valves direct fluid to specific components‚ while flow control valves manage the fluid’s speed. Pressure control valves maintain system pressure within safe limits. These methods ensure efficient energy transfer and system stability. Solenoid-operated valves enable automated control‚ enhancing precision and responsiveness. Proper control methods are crucial for optimizing performance‚ reducing wear‚ and ensuring safe operation in hydraulic systems.
Troubleshooting and Prototyping Hydraulic Circuits
Troubleshooting and prototyping hydraulic circuits involve identifying and resolving issues‚ ensuring efficient system performance. Step-by-step guides and diagrams aid in designing and testing circuits effectively.
8.1 Step-by-Step Guide to Prototyping Hydraulic Circuits
A step-by-step guide to prototyping hydraulic circuits involves planning‚ component selection‚ and assembly. Start by defining system requirements and creating a detailed diagram. Next‚ select compatible components such as pumps‚ valves‚ and actuators. Assemble the circuit‚ ensuring proper connections and fluid flow paths. Test the system under controlled conditions to identify and address any issues. Iterate on the design based on performance feedback to optimize functionality and reliability. This method ensures a systematic approach to building and refining hydraulic circuits effectively.
8.2 Common Issues and Solutions in Hydraulic Circuit Design
Common issues in hydraulic circuit design include fluid contamination‚ pressure drops‚ and overheating. These problems often arise from poor component selection or improper system layout; Solutions involve regular maintenance‚ such as filtering hydraulic fluids and ensuring proper valve sizing. Additionally‚ implementing pressure regulation and cooling systems can mitigate overheating. Addressing these issues early in the design phase prevents costly repairs and enhances system reliability and performance. Proper troubleshooting techniques and adherence to design best practices are essential for resolving and avoiding these common challenges effectively.
Hydraulic Schematics and Circuit Examples
Hydraulic schematics and circuit examples provide clear visuals of system components and their connections. They use standardized symbols and colors to represent fluid flow‚ pressure‚ and control elements effectively.
9.1 Examples of Basic Hydraulic Circuit Diagrams
Basic hydraulic circuit diagrams illustrate fundamental system configurations‚ such as simple fluid power circuits. These diagrams often include components like pumps‚ actuators‚ and valves‚ showcasing their connections. Visual representations use colors or patterns to depict fluid flow paths and pressure zones. For instance‚ a basic open-loop circuit might show a pump supplying fluid to a cylinder through directional control valves; These examples simplify complex systems‚ aiding in understanding and application. They are essential for educating beginners and prototyping new designs effectively.
9.2 Schematic Representation of Hydraulic Components
In hydraulic circuit diagrams‚ components are represented using standardized symbols‚ such as those outlined in ISO 1219-1. These symbols depict pumps‚ actuators‚ valves‚ and other elements‚ ensuring clarity. Lines and arrows illustrate fluid flow paths‚ while colors or patterns may denote pressure zones or fluid conditions. This visual language simplifies complex systems‚ aiding in design‚ troubleshooting‚ and maintenance. Schematics are essential for understanding how components interact and for documenting system architecture effectively. They provide a clear‚ concise way to communicate hydraulic system functionality.
Glossary of Hydraulic Terms
Hydraulic Circuit: A system of components like pumps‚ valves‚ and actuators working together. Hydraulic Fluid: Transfers energy in the system. Actuator: Converts fluid energy into motion. Pump: Generates fluid flow. Reservoir: Stores hydraulic fluid.
10.1 Key Terms and Definitions in Hydraulic Circuit Design
Hydraulic Circuit: A system of components like pumps‚ valves‚ and actuators working together. Hydraulic Fluid: Transfers energy in the system. Actuator: Converts fluid energy into motion. Pump: Generates fluid flow. Reservoir: Stores hydraulic fluid. Valve: Controls fluid direction and pressure. Cylinder: Produces linear motion. Pressure: Force per unit area in the fluid. Flow Rate: Volume of fluid moving per unit time. Symbols: Represent components in diagrams. Understanding these terms is essential for designing and interpreting hydraulic circuits effectively.